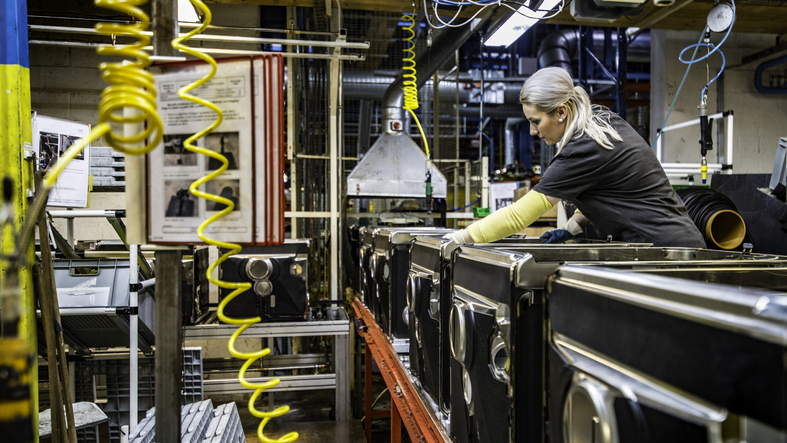
It’s safe to say that industrial supply chains have never been more complex. Much of this complexity can be attributed to a few key factors, including an increasingly global economy, the growing sophistication of manufactured goods and the large number of suppliers a typical company depends on to manufacture and bring its products to market. In many advanced industries, these numbers have reached unprecedented levels.
Take the automotive sector, for example. Research from McKinsey finds that auto manufacturers have on average 250 Tier 1 suppliers. Across the entire value chain, that number rises to 18,000 total suppliers. Similarly, the average aerospace company has 200 Tier 1 suppliers and a total of 12,000 across all tiers.
Further complicating matters—and increasing the risk to companies—is the global nature of these supply chains. While some geographical diversity may be beneficial, companies that are dependent on a single supplier from a single region for a particular component open themselves up to extreme levels of risk should that supplier be unable to deliver. And, for those companies with tens or hundreds of suppliers distributed across multiple geographical regions around the globe, their highly distributed supply chains are vulnerable to an almost endless array of potential disruptions, which can lead to delays, shortages and lost revenue.
The more complex the supply chain, the more moving parts, the greater the likelihood of major disruptions. And disruptions are costly. Research from the McKinsey Global Institute (MGI) has found that as much as 45 percent of one year’s EBITDA can be lost each decade as a result of disruptions.
The COVID-19 pandemic placed industrial supply chains under extreme stress
The hard-won experience supply chain planners gained during the COVID-19 pandemic perfectly illustrates the risks that companies face as their global supply chains continue to become more complex and the threat of disruption lurks around every corner.
Since March 2020, when the first wave of the pandemic hit, industrial supply chains have experienced a wide assortment of shocks, many of them severe and without recent historical precedent. Companies in virtually every industry have had to deal with some level of disruption to their supply chains as a result of COVID and have had no choice but to try and mitigate the impacts any way they can.
When the first government lockdowns were imposed in China, which makes up 28.7 percent of the total global output for manufacturing, workers were unable to go to work for many weeks. Production in numerous sectors critical to the world economy shut down completely, limiting the supply of many essential products and components available to manufacturers around the globe.
As the pandemic spread farther afield to Europe, North America and beyond, so did factory closures and supply challenges. Myriad delays and shortages ensued, some of which, such as a lack of ventilators and limited supplies of personal protective equipment (PPE), had dire consequences for COVID patients and health care workers, and took many months to resolve. Only furthering the complexity, many manufacturers, predominately automotive manufacturers, were called upon to make this needed PPE, causing huge shifts in production and sourcing.
More than 21 months later, major shortages persist in some manufacturing sectors. An ongoing global semiconductor shortage, for example, is preventing dozens of industries from getting their products to market and putting downward pressure on revenues. Consumer products, life sciences and tech industries have all been hard hit, but none more than the automotive industry, which is expected to lose up to $210 billion in revenue in 2021 alone.
What the pain of the COVID economy has hammered home for supply chain planners in the manufacturing sector is that future disruptions are inevitable and shouldn’t be viewed as one-offs, but rather as the status quo. Whatever the source of the disruption—an extreme weather event, a global financial crisis, a military conflict or a devastating cyberattack—planners need to continue their efforts to make their supply chains more resilient without reducing their ability to compete.
The time is now to make supply chains more resilient
As the global economy continues its slow recovery from the chaos unleashed by COVID-19, now is the time for companies to systematically stress-test their industrial supply chains to ensure they are resilient enough to handle whatever disruption comes next. After enduring the supply chain hardships of the pandemic, executives who say they expect to increase their company’s resilience by rebalancing their supply chains has increased from 70 percent to 93 percent.
What’s the best way forward and what steps should companies be taking to make their supply chains more resilient? Diversifying their supplier base is one key action companies can take to improve resilience, as is increasing production agility through automation and digitization in manufacturing. Another critical step in this process involves adopting sophisticated digital tools to provide better end-to-end visibility in supply chains, increase the accuracy of forecasting and improve sales and operations planning (S&OP) processes.
Companies that adopt specialized digital planning tools and dashboards enjoy real-time, end-to-end visibility into their supply chains, which is essential for managing risks and complexity. And, by implementing more advanced forecasting tools, planners gain greater insight into the bigger demand picture and can improve long-range forecast accuracy with advanced statistical forecasting.
Establishing and maturing S&OP processes based on industry best practices can also limit the impacts of disruptive factors beyond the control of supply chain planners. Not only do companies with higher S&OP maturity see improvements to their overall operational effectiveness, but they also make more confident decisions faster, which helps drive profitability.
To learn how one automotive company leveraged digital planning tools to mitigate supply chain complexity, watch the webinar Volvo Penta: Sailing Through Complexity with Agility.
Leave a Reply