Amid the COVID-19 situation, we held the first joint IBM-Kinaxis webinar session in Taiwan on May 12, 2020 which attracted more than 170 attendees. The theme of the webinar was "As smart manufacturing evolves again, what will be the new normal for intelligent production chains?"
The event featured Charles Wu, Senior Managing Consultant from IBM GBS Taiwan and Peng Shi, Industry Principal APAC from Kinaxis respectively.
Over the past six months, due to disruption such as trade wars and COVID-19, the global manufacturing sector has been dramatically impacted. Many business leaders view the past 180 days like a disaster movie with no end in sight. To help manufacturing enterprises better handle current and future disruptions, IBM and Kinaxis came together to share their best practices in supply chain.
Some of the discussion is highlighted below.
Managing the Sino-US trade war amidst the pandemic
What impact has Taiwan's manufacturing industry faced? What kind of challenges does the Sino-US trade war bring to the manufacturing industry? Have you seen what strategies the company has adopted?
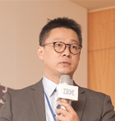
Charles Wu: Over the past two years, the Sino-US trade conflict has continued to affect each country’s tariffs strategy. Although the trade negotiations between Sino-US have stalled due to the novel coronavirus pandemic, it is expected that the pandemic will become another fuse, exacerbating tensions between the two sides. The industrial divisions of the two sides are alienated, and technology is more divergent. Under the support of huge domestic demand markets, the two countries have formed the so-called US regulations and China regulations.
In the early wrestling between the two parties, Taiwanese companies used to manufacture mainly in mainland China. In the continuous rise of the US-China trade war, many Taiwanese companies began to shift production bases back to Taiwan to alleviate customers’ concerns about tariffs. Outside of Taiwan, Southeast Asia and even India are the targets of the current transfer of Taiwanese companies.
The coronavirus outbreak caused more than 80 cities in mainland China to implement closed or semi-closed management. The resumption of work in major cities was not very smooth. When the lockdown was about to be further relaxed, the large-scale outbreak in March further exacerbated the situation.
Due to the pandemic, the closure of major cities has caused turmoil in the global market. The coronavirus has caused unprecedented damage to human health and the industrial supply chain; this wave of pandemic not only tests the medical systems of various countries, but also makes the supply chains of global companies face difficult crisis management decisions. Wharton School at the University of Pennsylvania professor Morris Cohen said that companies have to re-examine their own series of supply chain issues, such as whether they should expand their supply sources or increase the proportion of localized procurement. If you want to survive the crisis, how many raw materials, semi-finished products or other finished products should a company reserve?
This pandemic has also made companies realize that it is necessary to take proactive measures to reduce supply chain risks before the storm because it takes a long time to confirm whether many strategies can be implemented or are feasible. At a substantive level, it is not an easy task to reduce supply chain risks by adding new suppliers or local procurement. For example, the automotive industry is faced with the vast majority of components which are made in China.
Predicting supply and demand during periods of high uncertainty
During this period, what are the supply chain issues that the manufacturing industry is most concerned about? What are the most common and difficult challenges?
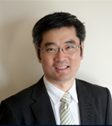
Peng Shi: The most common and difficult challenges faced by manufacturing companies can by categorized as follows:
From the short term perspective, there are several problems brought about by the Sino-US trade war. This includes how to determine the impact of tariffs, exchange rate changes on product gross margins and adjustment of pricing strategy. For example, price increases may affect sales volume, but without raising prices, profit margins are impacted.
Another short-term question is the need to assess the impact of US high-tech product import and export restrictions. For example, companies in the semiconductor industry need to assess the proportion of U.S. products or technologies used in their product composition to determine whether their product sales will have a substantial impact on customers from mainland China.
The short-term problems brought about by the pandemic are more about how to solve the current mismatch between supply and demand. Some companies will face a sudden rise in demand, such as those related to medical products. Some companies will face a sudden decrease in demand, such as the automotive industry.
On the supply side, many companies face the problem of supply cuts. We have a customer in the EMS industry headquartered in the United States. They have thousands of suppliers from mainland China. After the outbreak of COVID-19, the main problem they faced was the ability of suppliers to continue to supply, especially small suppliers. Because of some suppliers' relatively weak financial base and limited financing capacity, they may not survive this difficult period and may cease operations.
On the logistics side, issues include the reduction of cross-border routes and the sharp increase in transportation costs. We also need to understand the real needs of customers. Customers may exaggerate their actual needs because of panic behavior, thereby causing damage to the supply chain.
From the long-term perspective, the concern of enterprises is how to adjust their supply chain design in the future to deal with increasing risks and uncertainties. There are many factors which they will need to consider. For example, whether to continue to maintain factories on the mainland, or relocate part of the production capacity to Southeast Asia or other nearshore countries; whether it is necessary to develop alternative suppliers; what is the cost of migration; future market potential of relevant countries, tariffs, exchange rates, and trends in government preferential policies; etc. These require the simulation of various scenarios to make a judgment about the pros and cons of each.
By diversifying the combination of customers and products, enterprises can offset the risks caused by uncertainty. As the person in charge of the supply chain, it is necessary to consider whether the existing supply chain operation model is scalable and whether it can support adjustments flexibly and quickly.
No matter the challenge, agility matters
Manufacturing will continue to be among the industries which will be negatively impacted by the novel coronavirus pandemic.The virus will disrupt demand and supply behavior and thus affect the delivery of goods to consumers. However, companies that can know sooner and act faster will have an advantage. Those that adopt an agile approach to planning will be able to respond quickly to changes, no matter how they impact the wider supply chain network.
Learn more about planning for the new normal in our upcoming Kinaxis Live event.
Leave a Reply